Bringing innovative supply chain solutions to Healthcare Organizations utilizing Demand Planning technology and Lean management processes.
Tried the traditional cost-saving processes but frustrated because the results are still falling short of desired outcomes; looking for a better way? Gemstone Innovations uses your supply chain as a source of innovative cost-saving strategies. Let’s talk.
We offer a fresh new approach to the world of Healthcare Supply Chain that is consistent with and continues to evolve with the ever-changing healthcare delivery system. Utilizing Gemstone Innovation's ClinOps© system, your Supply Chain becomes seamlessly integrated into healthcare delivery.
Reduce Waste and Inefficiencies
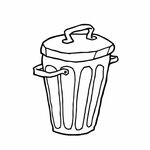
Using Lean processes with its ClinOps© program Gemstone Innovations’ primary operational focus to its clients is to add value to its operations by reducing supply waste and the associated process inefficiencies of acquiring and utilizing supplies.
Reduce Costs and Uncertainties
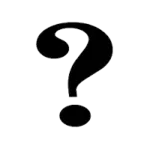
Gemstone Innovation’s ClinOps© program bridges clinical operations information (scheduling and supply menus) and MMIS (supply, usage, and purchasing information). The bridge reduces the time and associated costs involved in reformatting the same information into separate IT systems, thus making the flow of information more efficient.
Supply Chain staff utilizing Demand Planning processes can reduce the uncertainties in the supply chain. It becomes possible for all parties, from the users to the manufacturers, to see the demand, supply status, and availability of products throughout the complete chain. This process applies to commodity supply replenishment and, most importantly, focuses on procedure-specific products with high value, high cost, and variable usage. Reducing the usage uncertainties of these products is a major factor in managing the cost of these products.
Improving Cash Flow and Net Margins
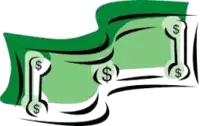
Gemstone Innovation's primary financial focus to its clients is their realization of an improvement in their cash flow: i.e, achieving an optimized inventory that frees up cash that had previously been tied up in supplies; as shown by an improved net margin and an improved debt to equity ratio. Money that is tied up in supplies makes that ratio less favorable. Using Demand Planning in your Inventory Optimization process has been shown to improve that ratio, thus enabling institutions to be eligible for more favorable interest rates.
Improving the Strategic Planning to Operations Execution Process
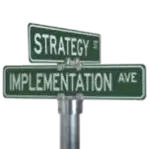
If you’re focused on your supply chain as providing your institution with the right product at the right price in the right place at the right time in the right quantity, then there is no wonder why your traditional cost-saving processes are falling short. The full potential of your supply chain function is not being realized.
At Gemstone Innovations, we consider the Healthcare Supply Chain in assisting clinicians make sick people well. Our primary focus is on the patient and supporting the staff serving the patient. Instead of focusing on a single dimension of the supply chain, such as the financial impact of optimizing the inventory, we consider how that dimension fits into the institution's business and clinical objectives.
Contact
Mr. Saphir is a change management consultant with a focus on Healthcare Supply Chain. He has spent 30+ years on the cutting edge of innovation to improve operational efficiencies and reduce waste in the supply chain. He has provided the leadership developing staff to achieve supply cost savings, improve customer service, and improve financial margins.
He is currently specializing in utilizing demand planning techniques and lean performance improvement processes to build trust relationships and finding creative solutions to inventory optimization and Perioperative Materials Management.
Before forming his own consulting firm, William H Saphir, LLC, he worked at Owens and Minor as a Consultant; was a Senior Logistics Consultant with Cardinal Health; an Assistant Vice President for an urban teaching IDN which included a 450-bed hospital, a Rehabilitation Hospital, 13 free-standing clinics, and an Ambulatory Surgical Center; and was a Director of Materials Management for a 730-bed urban teaching hospital.
Mr. Saphir earned a BS degree from University of Wisconsin; a MA degree from The University of Chicago; and a MBA from Loyola University Chicago.
Phone: 503.449.2320
Email: billsaphir67@gmail.com